What is the theory of constraints?
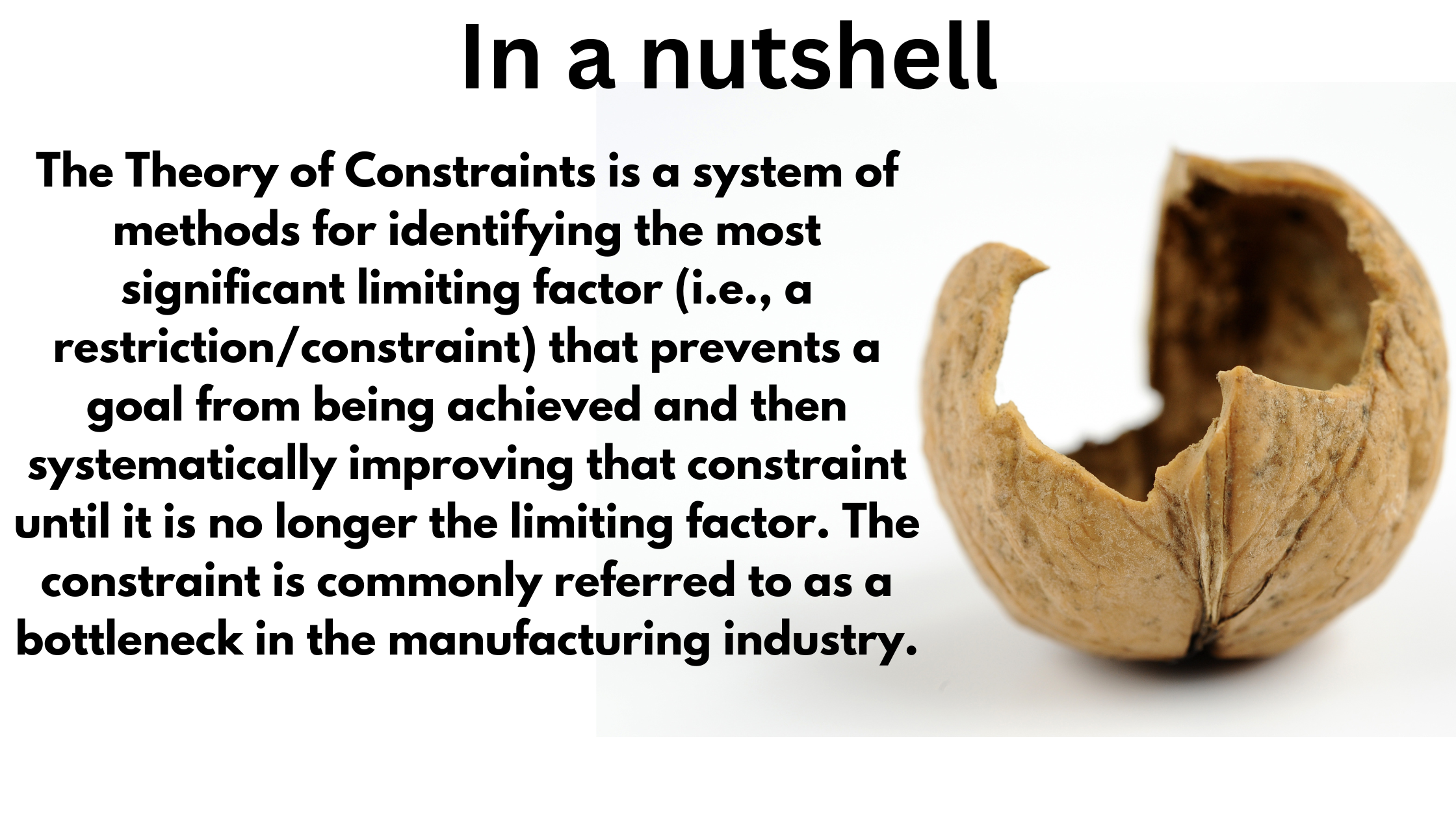
The Theory of Constraints (TOC) is a methodology for improving and identifying constraints in a business or any environment working to achieve a goal. A system constraint, also known as a "Bottle Neck," is a term used in many organisations today to describe when work is being held up or delayed in completion. When dealing with constraints, organisations will eventually achieve and fulfil their goals, which will deliver on customer expectations, improve processes, reduce lead time, and profit financially from a service provided.
Each system has a limitation or restriction. In most cases, the quickest and most efficient method to increase profitability is to concentrate improvement efforts on finding better ways to leverage this restriction.
How can The Theory of Constraints benefit an organisation?
- Improve the operations of a business
- Reduce constant firefighting
- Improve the relationship between employees and teams.
- Customer satisfaction
- Gaps are identified where the resource is required
The weakest link in the chain
Any chain's weakest link determines how strong it is overall. Similar to this, each system needs a limitation to set a maximum output. No system has endless output, therefore we are aware of this. For instance, no business will ever have unlimited sales revenue or high profit!
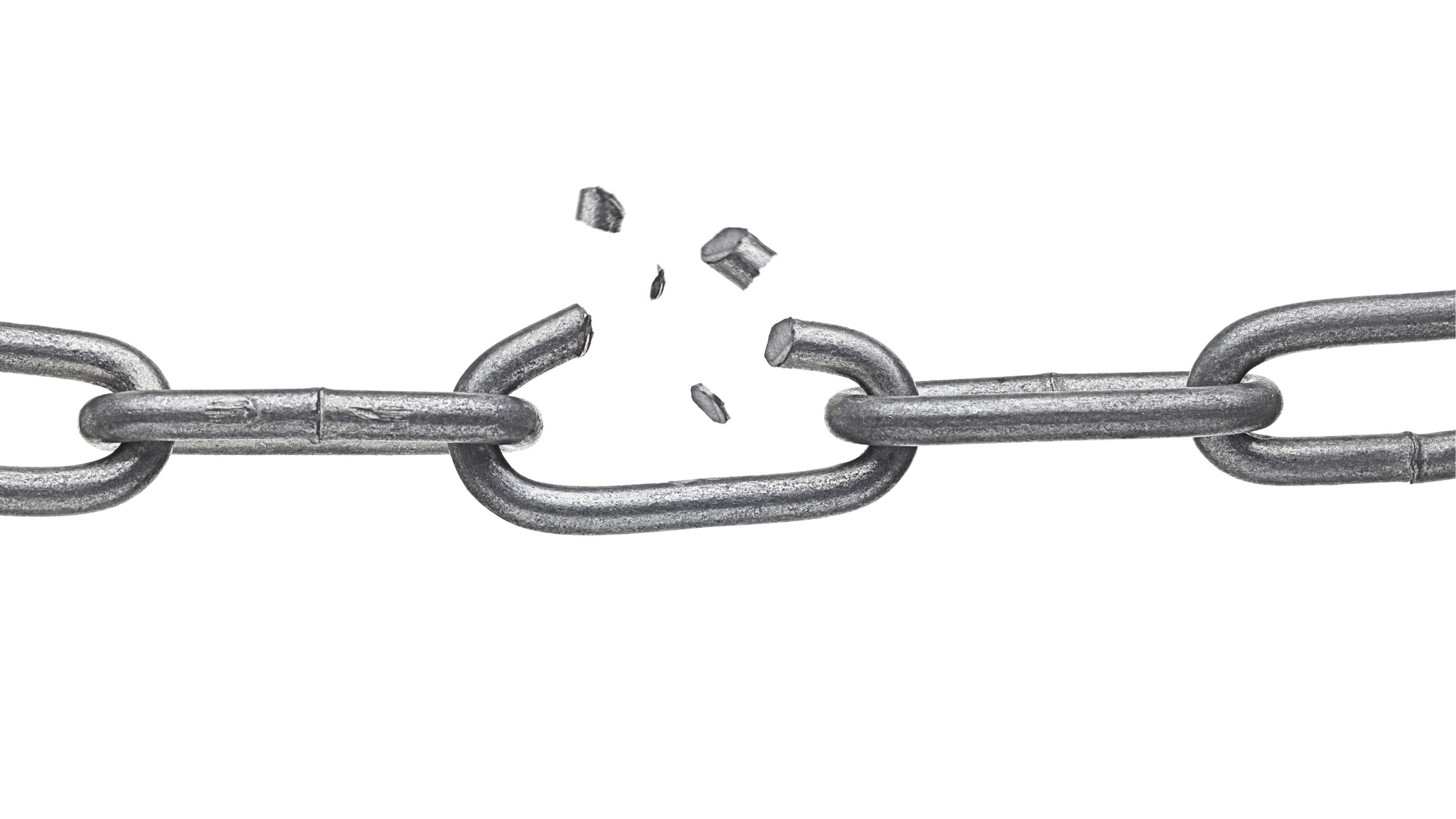
A chain will always have ONE (and only ONE) weak link.
Because they are not the weakest links in the chain, strengthening the others will never boost the chain's overall strength. In fact, due to the increased weight, strengthening a non-weakest link is likely to reduce the chain's total strength:
Similar to this, attempts to optimise each distinct process and function frequently overlook the influence on the limitation, leading to a number of unanticipated issues that lower the organization's overall performance and effectiveness.
For instance, optimising production output might lead to overproduction if sales orders are the limitation.
Such significant excess finished goods inventory will result in high carrying costs and capital costs.
A subsequent financial crunch could also cause delays in vendor payments, resulting in supply issues that delay orders, damage the company's reputation with clients, and lower future sales.
When using Theory of Constraints , management focuses on maximising the flow of throughput produced by the entire system rather than on optimising individual assets, functions, and resources.
The main procedures of The Theory of Constraints are centred on removing hurdles that stand in the way of each component operating as a consolidated whole.
The Theory of Constraints inherent ability to prioritise impevement initiatives is one of its enticing features.
The current limitation is always given top priority. Theory of Constraints is a highly concentrated methodology for generating rapid improvement in contexts where there is an immediate demand for improvement.
The five key steps
1) Identify the constraint
It is essential to remove the bottleneck in place if you are to succeed in your mission. However, until you are certain of what the bottleneck is, it cannot be reduced.
Finding your bottleneck could be simple in some situations. It might not be as evident in other situations. Finding the phase in your process that takes the greatest amount of time is one of the simplest places to start because it may be where things are getting stuck.
Additionally, it's critical to keep in mind that a constraint is essentially anything that is outside your control. Your conveyor belt, for instance, can only provide one meal plate at a time. There isn't a clear action you can take to alter that.
2.) Utilize the constraint
It's time to take use of your constraint now that you are aware of it.
This phase involves making sure that you are currently utilising the constraint to its fullest extent, which may sound harsh. Look closely at your restriction to see if you can improve it in any obvious ways.
EXAMPLE:
Surely only one meal plate can be provided at a time on your conveyor belt, right?
Or are you lacking a component
3.) Subordinate everything else to the constraint
Understanding the constraints themselves was the focus of the previous phase; in this step, we will learn about the constraints' surroundings. Make sure everything feeding that restriction is operating at maximum capacity as well. To be used as effectively as feasible, your constraint should receive exactly the number of resources from non-constraints that it requires.
For instance, are the meal plates arranged such they can be passed through the machine as quickly as possible adjacent to the conveyor belt?
4.) Promote the constraint
Time to talk about the limitation itself now. How might the bottleneck you discovered be made more capable? In many instances, this will include giving it a boost with more resources.
These might include, to mention a few, extra personnel, resources, or tools.
Example: To expedite this project and any upcoming meal servings to the client, you decide you need to buy two more conveyor belts.
5.) Avoid idleness and repeat the process
Your crew is moving quickly through those plate meals now that you've solved the constraint.
Your labour of love is finished, right? Nowhere near. Constant process improvement is the core concept of the idea of limitations. This implies that after removing one constraint, you'll inevitably find another.
To find the next limitation and prevent idleness, you should retrace your steps (meaning you want to avoid becoming complacent).
Example: You find you don't have enough team members to operate the extra conveyor belts given your increased conveyor belt capacity.